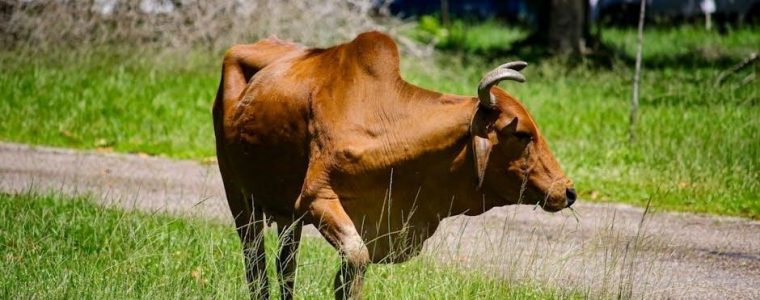
tabla de amperaje para soldar pdf
Welding amperage tables provide essential guidelines for selecting the optimal current settings for various welding processes and materials, ensuring strong and consistent welds․ These tables are crucial for welders to achieve precise control over the welding process, helping to avoid defects and improve overall weld quality․ They are widely available as PDF guides, offering detailed charts and recommendations for different electrode sizes, material thicknesses, and welding techniques․
1․1 What are Welding Amperage Tables?
Welding amperage tables are detailed guides that provide recommended current settings for various welding electrodes, materials, and thicknesses․ These tables typically include charts and diagrams that list the optimal amperage ranges for different electrode sizes, ensuring proper fusion and penetration․ They serve as a quick reference for welders to select the correct current for their specific application․ For example, a 0․045-inch electrode might require 140-160 amps, depending on the material and welding process․ These tables are often available in PDF formats for easy access and use․
1․2 Importance of Amperage in Welding
Amperage plays a critical role in welding as it directly affects the quality and strength of the weld․ Proper current settings ensure adequate heat input, necessary for melting the electrode and base material uniformly․ Incorrect amperage can lead to defects like lack of fusion or porosity, compromising the weld’s integrity․ Using the correct amperage helps maintain the mechanical properties of the material, ensuring durability and safety in the final product․ Referencing welding amperage tables is essential to achieve optimal results and avoid common welding errors․
Understanding Welding Processes and Amperage Requirements
Welding processes like MIG, TIG, and MMA require specific amperage settings to ensure proper fusion and quality․ Correct current selection is vital for achieving strong, defect-free welds consistently․
2․1 MIG/MAG Welding Amperage Ranges
MIG/MAG welding typically operates within amperage ranges of 30 to 600 amps, depending on material thickness and wire diameter․ Thinner materials require lower currents, while thicker materials demand higher amperage to ensure proper penetration․ Wire diameters, such as 0․045″ or 1․2 mm, also influence current settings․ Voltage plays a crucial role, with ranges between 16-30 V, affecting arc characteristics․ Proper amperage selection prevents issues like lack of fusion or excessive heat input, ensuring high-quality welds across various applications․
2․2 TIG Welding Amperage Requirements
TIG welding typically requires amperage settings between 30 to 300 amps, depending on material thickness and type․ Thinner materials like aluminum or stainless steel may use lower currents, while thicker steels require higher amperage for proper penetration․ Electrode size, commonly ranging from 1/16″ to 1/4″, also influences current selection․ Voltage settings generally range from 10 to 20 volts, ensuring a stable arc and precise control․ Proper amperage adjustment is critical for avoiding defects and achieving high-quality welds in TIG processes consistently․
2․3 Arc Welding (MMA) Amperage Settings
Arc welding (MMA) typically operates within an amperage range of 30 to 300 amps, depending on the electrode size and material thickness․ Thicker materials require higher currents for proper penetration, while thinner materials need lower settings to prevent burn-through․ Electrode diameters, commonly ranging from 1/16″ to 1/4″, also influence the current selection․ Consulting amperage tables ensures optimal weld quality and helps avoid defects by providing precise settings for various applications․
Factors Influencing Amperage Selection
Material thickness, electrode diameter, and voltage are key factors in determining the optimal welding current․ These elements collectively influence heat input, penetration, and overall weld quality․
3․1 Material Thickness and Amperage
Material thickness directly impacts welding amperage requirements․ Thicker materials typically need higher current to ensure proper penetration, while thinner materials require lower settings to prevent burn-through․ For example, a 0․045-inch wire might operate between 140-160 amps for thin materials and 220-240 amps for thicker ones․ Adjusting amperage based on material thickness ensures optimal weld quality and prevents defects․ Always consult amperage tables for specific material thickness ranges to achieve the desired results․
3․2 Electrode Diameter and Welding Current
E electrode diameter plays a crucial role in determining the appropriate welding current․ Thicker electrodes generally require higher amperage to achieve proper melting and penetration, while thinner electrodes need lower settings to avoid overheating․ For instance, a 0․045-inch wire might operate at 140-160 amps, increasing to 220-240 amps for larger diameters․ Consulting amperage tables helps match the electrode size to the correct current, ensuring efficient and high-quality welds without damaging the electrode or the base material․
3․3 Voltage and Its Role in Welding
Voltage plays a critical role in welding, as it influences the shape and stability of the arc․ Typical voltage ranges vary depending on the welding process, with MIG/MAG often operating between 14-28 V and TIG requiring 10-24 V․ Higher voltage increases arc penetration but can also raise heat input, potentially warping thin materials․ Proper voltage setup ensures a consistent arc, which is essential for achieving high-quality welds․ Referencing amperage tables helps welders balance voltage and current for optimal results across different materials and thicknesses․
Safety Guidelines for Welding Amperage
Proper amperage settings prevent electrical hazards and overheating․ Always use correct voltage and current for your electrode and material to ensure safe welding practices and equipment longevity․
4․1 Personal Protective Equipment (PPE)
Wearing proper PPE is crucial for safety during welding․ This includes helmets with shaded lenses to protect eyes from UV light, heat-resistant gloves to prevent burns, and fire-resistant clothing․ Steel-toe boots and leather aprons add extra protection․ Ensuring all PPE is worn correctly helps prevent injuries from sparks, spatter, and electrical arcs․ Never weld without proper gear, as it safeguards against severe burns and eye damage from the intense welding arc and flying particles․
4․2 Proper Ventilation and Workspace Setup
Proper ventilation is essential to remove welding fumes and particles, ensuring a safe working environment․ The workspace should be free from flammable materials and well-ventilated to prevent the accumulation of hazardous fumes․ Using exhaust systems or fans can enhance airflow, reducing the risk of inhalation․ Keeping the area clean and organized prevents tripping hazards, while maintaining a safe distance from flammable materials minimizes fire risks․ Adequate lighting is also crucial for clear visibility during welding tasks․
4․3 Electrical Safety Precautions
Electrical safety is critical in welding to prevent shocks and fires․ Always use properly insulated cables and ensure all equipment is grounded․ Avoid welding in wet conditions or near water, as moisture increases the risk of electrical hazards․ Regularly inspect welding machines and cables for damage or wear․ Keep flammable materials away from the welding area to minimize fire risks․ Never touch electrical components with wet hands or while standing on a conductive surface․ Ensure proper installation and maintenance of electrical equipment to maintain safety standards․
Reading and Interpreting Amperage Tables
Amperage tables guide welders in selecting optimal current settings based on electrode classification, material thickness, and welding processes, ensuring precise control for high-quality, consistent welds․
5․1 Understanding Electrode Classification
Understanding electrode classification is crucial for interpreting amperage tables․ Electrodes are classified based on their flux coating and intended use, with specific types suited for different materials and welding processes․ For example, electrodes for mild steel, stainless steel, or aluminum each have unique properties․ Referencing the classification helps match the electrode to the correct amperage range, ensuring proper fusion and weld quality․ Tables often list electrode diameters and their corresponding amperage ranges, guiding welders in selecting the right settings for their application․ This alignment is essential for achieving consistent, high-quality welds across various projects․
5․2 Matching Amperage to Electrode Size
Matching amperage to electrode size is critical for achieving optimal weld quality․ Welding amperage tables provide detailed guidelines, listing recommended current ranges for specific electrode diameters․ For example, a 0․045″ electrode might require 140-160 amps, while a 1/8″ electrode could need 200-240 amps․ Proper alignment ensures efficient fusion and penetration, avoiding defects like lack of fusion or burn-through․ Referencing these tables helps welders select the correct settings, ensuring consistency and quality in their work․ This step is fundamental for mastering welding techniques and materials․
5․3 Adjusting Amperage for Different Materials
Adjusting amperage based on material type and thickness is essential for optimal welding results․ Thicker materials generally require higher amperage for proper penetration, while thinner materials need lower settings to prevent burn-through․ Welding amperage tables, often available as PDF guides, provide detailed recommendations for various materials, ensuring the correct current is used․ This customization helps achieve strong, defect-free welds and maintains the integrity of the material being welded․
Practical Applications of Amperage Tables
Amperage tables guide welders in selecting optimal current settings for various materials and thicknesses, ensuring proper penetration and weld quality in real-world applications․
6․1 Welding Thin Materials
When welding thin materials, lower amperage settings are crucial to prevent burn-through and distortion․ Tables provide precise current ranges, such as 140-160A for 0․045″ wires, ensuring proper fusion without excessive heat․ This helps maintain material integrity and avoids warping․ Proper technique, like shorter arc lengths and reduced voltage, complements lower amperage for thin sheets․ Using these guidelines ensures high-quality, defect-free welds in delicate applications, making amperage tables indispensable for thin material welding projects․
6․2 Welding Thick or Structural Materials
For thick or structural materials, higher amperage settings are essential to achieve full penetration and strength․ Tables provide specific current ranges for different thicknesses, ensuring weld integrity․ Higher currents help fusion deeper into the material, avoiding lack of penetration defects․ Proper joint preparation and electrode selection are also critical․ Using the correct amperage ensures robust welds in heavy-duty applications, maintaining the structural integrity of the material while preventing defects like porosity or incomplete fusion․
6․3 Optimizing Weld Quality with Correct Amperage
Correct amperage ensures optimal weld quality by achieving proper penetration, fusion, and aesthetics․ Tables guide welders to select the right current for specific materials and thicknesses, preventing defects like distortion or lack of fusion; Adequate heat input, controlled by amperage, ensures strong and durable joints․ By adhering to recommended settings, welders achieve consistent results, enhancing both the structural integrity and appearance of the weld․ Proper amperage adjustment is key to mastering high-quality welding outcomes․
Common Mistakes to Avoid
Common errors include using incorrect amperage for material thickness, ignoring electrode size recommendations, and improper voltage adjustments, leading to poor weld quality and potential safety risks․
7․1 Using Incorrect Amperage for Material Thickness
Using the wrong amperage for material thickness leads to weak or brittle welds, poor penetration, and increased risk of weld failure․ Always consult amperage tables to ensure the correct current matches the material’s thickness and electrode size․ Incorrect settings can also cause excessive heat, warping, or lack of fusion․ Proper adjustment is crucial for achieving strong, durable welds and maintaining structural integrity․ Referencing detailed charts helps avoid errors and ensures optimal welding results․
7․2 Ignoring Voltage Settings
Ignoring voltage settings can lead to poor weld quality, inconsistent arc stability, and reduced penetration depth․ Voltage directly impacts the welding arc’s characteristics, and mismatching it with amperage can result in defective welds․ Proper voltage adjustment ensures optimal arc performance, avoiding issues like porosity or lack of fusion․ Always refer to amperage tables to balance voltage and current for the specific electrode and material being used, as incorrect settings can compromise weld integrity and strength․
7․3 Overlooking Electrode Diameter
Overlooking electrode diameter is a common mistake that can significantly affect weld quality․ Using the wrong electrode size for the chosen amperage can lead to insufficient penetration, poor fusion, or excessive heat input․ Amperage tables typically specify recommended current ranges based on electrode diameter, ensuring proper weld penetration and bead profile․ Ignoring this critical factor can result in defective welds and reduced structural integrity, emphasizing the importance of matching electrode size with amperage settings for optimal results․
Advanced Welding Techniques and Amperage
Advanced welding techniques like pulsed welding and digital machine usage optimize amperage control, enhancing precision and quality in specialized applications․
8․1 Pulsed Welding and Amperage Control
Pulsed welding employs intermittent current flow to enhance precision and reduce heat input, especially for thin or heat-sensitive materials․ Amperage control in pulsed modes allows for adjustable peak and background currents, optimizing weld penetration and aesthetics․ This technique minimizes distortion and improves weld quality in advanced applications․ Tables from PDF guides provide specific amperage ranges for pulsed welding, ensuring compatibility with electrode sizes and material thicknesses, making it a versatile option for specialized welding tasks․
8․2 Using Digital Welding Machines
Digital welding machines offer advanced control over amperage, allowing for precise adjustments to suit various materials and techniques․ These machines often feature preset amperage settings and real-time monitoring, ensuring consistent weld quality․ They are particularly useful for adhering to amperage tables, as they enable quick reference and implementation of recommended settings․ Digital technology enhances efficiency and accuracy, making it easier to achieve optimal welds for both standard and specialized applications, as outlined in welding amperage PDF guides․
8․3 Fine-Tuning Amperage for Specialized Joints
Fine-tuning amperage is critical for achieving high-quality welds in specialized joints, such as butt, lap, or corner joints․ Welding amperage tables provide detailed guidelines for adjusting current settings to match joint configurations and material properties․ By referencing these tables, welders can optimize penetration and fusion, ensuring strength and durability․ Techniques like pulse welding further enhance precision, allowing for tailored amperage control․ This level of customization is essential for meeting the demands of complex welding projects, as outlined in welding amperage PDF guides․
Referencing welding amperage tables ensures precise settings for electrodes and materials․ Always adhere to best practices, maintain consistency in weld quality, and continuously refine your welding skills․
9․1 Summary of Key Points
Welding amperage tables are vital for achieving precise current settings, ensuring strong and consistent welds․ They provide detailed guidelines for electrode sizes, material thicknesses, and welding techniques․ By referencing these tables, welders can avoid defects and improve weld quality․ Consistency is key to maintaining superior weld quality․ Continuous learning and skill refinement are essential for mastering welding processes․ Utilizing resources like PDF guides can further enhance understanding and application of amperage settings for optimal results․
9․2 Maintaining Consistency in Weld Quality
Maintaining consistency in weld quality requires precise amperage control, as outlined in welding tables․ Using the correct amperage for electrode size and material thickness ensures uniform weld penetration and appearance․ Regularly referencing amperage guides helps avoid variations in weld quality․ Proper workspace setup and consistent use of PPE also contribute to reliable results․ By adhering to recommended settings and adapting for specific materials, welders can achieve consistent, high-quality welds across various projects and materials․
9․3 Continuous Learning and Skill Improvement
Continuous learning is key to mastering welding techniques and amperage control․ Welders should regularly update their skills by consulting PDF guides, online tools, and welding communities․ Exploring advanced techniques, such as pulsed welding and digital machine settings, enhances adaptability․ Practicing with various materials and electrode sizes refines expertise․ Staying informed about new technologies and materials ensures welders remain competitive and capable of delivering high-quality results in evolving industrial environments․
Additional Resources
Explore PDF guides, online calculators, and welding forums for detailed amperage charts and expert advice․ These resources offer practical insights and tools for refining welding techniques and setups․
10․1 Recommended PDF Guides for Welding Amperage
PDF guides on welding amperage tables are essential resources for welders, offering detailed charts and practical advice․ These guides provide comprehensive tables for electrode sizes, material thicknesses, and welding techniques, ensuring accurate amperage selection․ They are widely available online and cater to both beginners and experienced welders, covering various welding processes like MIG, TIG, and MMA․ These guides are invaluable for refining welding techniques and achieving precise control over amperage settings for high-quality welds․
10․2 Online Tools and Calculators
Online tools and calculators are invaluable for determining precise welding amperage settings․ Websites offer interactive charts and calculators that allow users to input material thickness, electrode size, and welding process to find optimal amperage ranges․ For example, tools like “Welding Amperage Calculator” and “Amperage Chart Generator” provide instant results, helping welders fine-tune their settings․ These resources are particularly useful for adjusting to specific materials or techniques, ensuring efficient and high-quality welds without the need for physical tables․
10․3 Welding Communities and Forums
Welding communities and forums are excellent resources for sharing knowledge and best practices․ Platforms like WeldingWeb, Reddit’s r/welding, and specialized Facebook groups offer spaces for discussing amperage tables and techniques․ Experienced welders often share insights, troubleshooting tips, and recommendations for optimizing weld quality․ These forums also provide access to downloadable PDF guides, such as “Tabla de Amperaje para Soldar,” helping users find the perfect settings for their projects․ Engaging with these communities fosters learning and collaboration among professionals and hobbyists alike․